CAM Software for the Automotive sector
An optimal CAD/CAM system is a critical success factor.
The automotive industry is facing significant challenges, which are causing a tremendous upheaval in the industry.
In the highly competitive environment of the automotive industry, all manufacturers are under pressure to constantly bring new models to market: In addition to ever shorter innovation cycles, this also results in increasingly complex design requirements. The focus is therefore on short throughput times at the highest possible quality across all segments – from chassis, transmission, and engine construction all the way to manufacturing large fascia molds or stamping dies. The choice of the optimal CAD/CAM system is a critical success factor.
However, the challenge does not stop with the renewal and expansion of the model range. In addition, the automotive industry must also address topics such as lightweight construction, new technologies for autonomous driving, or the trend away from combustion engines towards hybrid engines.

Industry Challenges
-
High flexibility and delivery reliability
Short response times are of the essence
-
Reduced programming times
Based on automated NC programming for pockets and holes thanks to feature and macro technology
-
Reduced machining times
Innovative HSC and HPC strategies for roughing and finishing, from design studies for prototype construction through to small and large batches
-
Demanding materials
Milling that goes easy on tools and machines thanks to HSC and HPC strategies
-
High process reliability
Thanks to collision-tested toolpaths and state-of-the-art simulation technology
5‑axis Machining: Engine milling
Programmed by CAM software hyperMILL® – milled on a DMG-MORI machine.
A manufacturing example for Automotive.
Would you like to learn more about our complete CAM solution for the Automotive sector?
If so, please contact OPEN MIND Technologies USA, Inc.
1492 Highland Avenue, Unit 3, Needham MA 02492
hyperMILL® CAD for CAM (formerly hyperCAD®-S)
hyperMILL® is a “CAD for CAM” solution that strongly addresses the needs of the automotive industry. CAM programmers regularly face the same challenges: importing files of various formats that sometimes comprise vast amounts of data and preparing them for subsequent NC programming. hyperMILL® has a comprehensive interface package that CAM users can use to process a wide range of CAD formats simply, reliably, and quickly. With the analysis and repair function of the built-in CAD software in hyperMILL®, CAM-based part geometry changes, such as closing holes, can be implemented efficiently. Moreover, the filter and selection functions allow the NC programmer to constantly keep an overview of the entire project, even when processing very large components.
Fast, efficient, and precise machining with the hyperMILL® CAM software
To ensure short throughput times, a wide variety of workpieces must be machined quickly, efficiently, and with precision, while also maintaining the highest possible surface quality. The CAM solution from OPEN MIND generates NC programs that cover all of the requirements with ease!
The 5-axis strategies of hyperMILL® support positional or simultaneous machining. This means that shorter and thus more robust tools can be used. Also, unnecessary tool changes are avoided and setup times on the machine are significantly reduced. hyperMILL® MAXX Machining further reduces throughput times. A wide selection of HPC strategies for roughing and finishing result in enormous time savings when milling chassis, engine, or transmission parts. 5-axis tangent plane machining and the use of conical barrel cutters can reduce finishing jobs by up to 90 percent.
CAM Strategies for Industry-specific Components
hyperMILL® MAXX Machining
High-Feed Cutting (HFC)
Rest Machining
Special 5‑axis applications
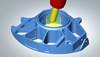
5-axis helical drilling
Using this strategy, the material is milled from a circular pocket based on helical milling in a 5‑axis simultaneous movement, which is particularly efficient and tool friendly, even when handling high-strength materials.Adaptive pocket/High-Feed Cutting (HFC)
hyperMILL® offers a large number of functions for HSC and HFC machining. Using a freely definable tool geometry makes it possible, for example, to precisely map high feedrate cutters, which are then taken fully into account during collision checks and rest material calculation. Machining times can be vastly reduced in connection with the ‘adaptive pocket’ function, which automatically identifies circular or rectangular pocket geometries in the area to be machined, as well as remaining rest material.
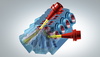
Tube package
The ideal solution for intake and exhaust tubes for engines as well as pipe inlets and outlets for pumps and compressors: 5‑axis tube machining makes it possible to machine strongly undercut geometries on the basis of the simplest guide curves. The proven collision check and avoidance system ensures safe 5‑axis milling operations.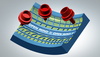
Tire mold package
The dedicated tire module mills tire molds more economically than ever before. Automations and special functions guarantee a simplified and efficient programming process, for example, for knife cuts, stone ejector functions, and other details. The tire clock considerably simplifies the programming of identical tire sections.
Impellers and Blisks
This special package allows for programming turbo components such as impellers and blisks even without special knowledge. The multi-blade package integrates automated functions to reduce the number of parameters to be entered to a minimum. Proven collision checking guarantees a very high level of process reliability.Many requirements – always the perfect solution
Whether elaborately designed rims, brake calipers, or large molds for cladding components: OPEN MIND’s innovative CAM strategies allow for milling and mill-turning a wide variety of automotive components, whether for a design study or series production.
hyperMILL® offers complete packages that address specific industry requirements. For example, the tube package can be used for machining intake and exhaust ducts in the engine block, and the tire mold package ensures maximum efficiency when milling engraved molds, tire models.
Automation made possible thanks to feature and macro technology
Time savings can be achieved during milling and NC programming. The hyperMILL® feature technology automatically detects component details such as holes and pockets with all their properties. These features can be used for highly automated NC programming by means of stored machining sequences, so-called macros. This intelligent way of automation and standardization significantly reduces the programming effort and reliably helps to avoid human errors.
Reliable simulation – reliable process
hyperMILL® offers a wide range of functions and applications that ensure maximum process reliability. hyperMILL® VIRTUAL Machining is a simulation based on the NC code. It allows users to map and control the entire process, including the entire machine environment starting with tool change positions. The simulation already captures and shows users the exact machine movements that will be later performed on the machine tool, which enables optimum collision control. In addition, numerous analysis and optimization functions contribute to the safe and reliable control and further improvement of the entire manufacturing process.
Advantages at a Glance
-
Reduced setup times
Complete and multi-axis machining using 5‑axis technologies
-
Shorter programming times
Automated NC programming thanks to feature and macro technology
-
Reduced machining times
Innovative HSC and HPC strategies for roughing and finishing
-
Improved process reliability
Thanks to collision-tested toolpaths and reliable simulations based on the NC code
-
Higher quality
Blending cycles result in optimized surfaces and reduce rework machining to a minimum