Kusters Precision Parts relies on hyperMILL® –
More flexibility and productivity with CAM
Kusters Precision Parts | Oss, Netherlands
Kusters Precision Parts specializes in the machining of complex, high-precision components used in the semiconductor, medical, optical and aerospace industries, among others. The manufacturer based in Oss, the Netherlands, supports its efficient and flexible production with 21 hyperMILL® programming stations.
Kusters Precision Parts was founded in 1973 as a manufacturer of high-tech components. Since then, the company has grown rapidly. So much so that in 2021, the company moved into a new location with a state-of-the-art production area of no less than 7,500m2 and its own 400m2 clean room. The machine park now consists of around 36 machining centers and 10 EDM machines, with more machines planned. In 2022 alone, 13 machine tools were purchased.
“We expect major industrial growth in the coming years, particularly from the semiconductor industry. We are investing in automation and process optimization. Various intelligent functionalities in the hyperMILL® CAD/CAM solution are helping to increase the efficiency of the programming process and therefore productivity.”
Olaf Heijers, Managing Director at Kusters Precision Parts.
Automation in the CAM area
One of the technologies that Kusters uses is the hyperMILL® AUTOMATION Center. Automation reduces programming times, standardizes processes and improves throughput times. The standard CAD/CAM automation of hyperMILL® enables the automated programming of similar geometries, recurring form elements and features such as holes or pockets as well as repetitive processes. The hyperMILL® AUTOMATION Center offers even more options for creating individual automation projects. For example, Kusters has digitized all fixtures and stored them centrally on the server. This allows the programmer to select a predefined fixture for each machine. As Heijers confirms, this standardization saves a lot of effort, as the components can be programmed and simulated within a very short time. In addition, the risk of human error is minimized as all employees involved work with the same data.
Full transparency
In addition to integrating all clamping operations into hyperMILL®, Kusters is also working on digitizing all of its machining tools. As the supplier strives for maximum flexibility, it has equipped most of its machine tools with large tool magazines that offer space for hundreds of tools. Structuring these is a challenge. Merging all tool data in a central tool library creates complete transparency in tool management. This also has the advantage that everyone in the company works with the same tool parameters. This in turn speeds up the programming and production process and reduces the risk of errors.
"The aim is to make all data that is important for the production process centrally accessible. In this way, we not only reduce the susceptibility to errors, but also build up a knowledge database. In practice, you often see that people work with different tool parameters. Some are careful and work with too low a feed rate, while others overload the tool. By using a central database with defined parameters, programmers know which data they need to work with. This is also important for the future, as expertise is slowly being lost due to the low number of new technicians. To be able to continue manufacturing our high-tech products in the future, we therefore need to retain specialist knowledge and standardize processes as much as possible," says Johan van den Heuvel, the Milling Team Leader at Kusters Precision Parts.
Simulation provides certainty
Stefan van Aalst, Director of OPEN MIND Benelux, adds: "The moment all data from machines, fixtures and tools are digitally available, it is possible to perform a reliable simulation. hyperMILL® VIRTUAL Machining enables communication with the machine and offers us a simulation accuracy that corresponds to the real machine. When the NC program is generated, our VIRTUAL Machining knows the CAM programming on the one hand and all machine specifications and restrictions on the other. This allows us to optimally adapt the movements to the machine during NC code generation, find the best settings and eliminate unnecessary movements. All in all, this not only avoids collisions but also optimizes the NC program, resulting in shorter machining times."
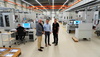
Stefan van Aalst, OPEN MIND, Olaf Heijers and Johan van den Heuvel (from left to right) in the modern, automated workshop at Kusters Precision Parts. The hyperMILL® programming stations can be seen in the background. Image: Kusters Precision Parts
Always up-to-date
van den Heuvel has worked with various CAD/CAM packages in the past but was ultimately impressed by the performance of hyperMILL® and in particular the ease with which 5-axis NC programs can be generated.
van den Heuvel adds: "We mainly manufacture complex parts that regularly require 5-axis machining. As we produce individual parts and small batches, the speed of programming is crucial for meeting short delivery times. In addition, we cannot afford any inaccuracies, as we work for very demanding industries. With the various five-axis strategies in hyperMILL®, we can program complex geometries, free-form surfaces and deep cavities quickly and easily."
According to Heijers, many new functionalities have been added since Kusters introduced hyperMILL®. "We are in the top segment and are always looking for solutions to automate and optimize processes even more. If you don't do that, you won't get anywhere." van den Heuvel continues: "Because developments are happening at a rapid pace, it's a challenge to keep up. OPEN MIND therefore offers training courses twice a month in which the latest hyperMILL® functionalities are presented. This is a real added value. We have already benefited a lot from VIRTUAL Machining. For example, we are currently keeping a very close eye on PMI developments. We also really appreciate the fact that we can rely on a partner who supports us with both knowledge and service."