MKW & OPEN MIND Helps Bluebird to Sail Again
MKW Engineering Ltd. | Tyne Tunnel Estate, North Shields, United Kingdom
2006 a team of engineers and enthusiasts decided to rebuild the famous craft Bluebird K7, a project that has enlisted the charitable support from companies in the North East. The re-build project is approaching completion credit to manufacturers like MKW Engineering that are utilising high end CAM software from OPEN MIND Technologies.
MKW Engineering was formed in 1976 and, over the years, the company has established an extensive blue chip client base in industrial sectors as varies as subsea, defence, nuclear, aerospace and petrochemical sectors. MKW joined Pryme Group in 2015.
MKW acquired its first 5-axis machine tool over ten years ago to accommodate its increasingly complex workload and to reduce cycle times on its large parts with small batch sizes. With high material costs on large parts and the overall value of components after machining exceeding £25,000, getting the job 'right fist time' takes on a new level of importance.
As MKW's Sales & Commercial Director, Mr Rahmon Nassor comments: “We have invested over £6m in ten years on machine tools. With continued investment in machine tools, our CAM package was creating problems as the postprocessors were incapable of supporting the complex tool paths on our 5-axis investments. This created scrapped parts, tool breakages, machine crashes and a culture of nervousness. Additionally, the package couldn't keep up with our high workload of one-off or small batch production of complex parts.”
“Depending upon the features of each component, hyperMILL® has reduced our programming times on average from 30 to 50%.“
Rahmon Nassor, Sales & Commercial Director
Exceptional results
“We knew we needed a new CAM package and with recommendations from numerous machine tool installation engineers and our own investigation of 3 leading vendors, we opted for OPEN MIND's hyperMILL®. The results have been exceptional.”
As soon as hyperMILL® was installed, the benefits arrived in abundance. Firstly, the ability to simulate part production prior to any physical cutting gave the programmer confidence that parts were not going to be scrapped. This confidence was backed by OPEN MIND’s ability to supply postprocessors for each individual machine to ensure the part programmed on screen was exactly what would be cut by the machine.
Manufacturing Donald Campbell’s Legacy
The feature recognition has proven of major benefit on the sponsons manufactured for the Bluebird K7 project. Each of the two 1.8m long aluminium sponson parts has over 480 holes of differing diameters and hyperMILL® reduces the tool changeovers and optimises tool paths with its feature recognition cycle.
However, a key feature of hyperMILL® that has proven a huge success for MKW is the mirroring function. This feature enables the programmer to mirror a program in all axes for left or right hand parts.
Customer Story
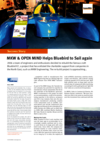
MKW Engineering Ltd.
Tyne Tunnel Estate, North Shields, UK