Reliably Machine Rib Geometries
Volkswagen AG – Component Tool Engineering | Braunschweig (Lower Saxony), Germany
Programming rib geometries is not an easy task. By working together with OPEN MIND, Volkswagen was able to develop a feature to program rib geometries in a highly efficient manner. This function automatically detects grooves to be milled. Steep areas and floors are machined separately.
An impressive production portfolio and effectiveness and efficiency in the CAD/CAM process chain make VOLKSWAGEN AG in Braunschweig a technological pioneer in component tool engineering. Here, the company manufactures moulds for cylinder heads and chassis, die cast moulds for gearboxes, coupling housings and steering boxes and compression tools for reshaping the thick sheet metal of the chassis and injection moulds, for example, for bumpers or instrument panels made from plastic.
Long-standing development partnership
“We opted for OPEN MIND back in 2002 because hyperMILL® best supports our standardisation approach“, says Jörg Wenserski, Head of Engineering at the Machine Centre. “This has led to the development of a productive partnership with OPEN MIND and as a result, we have achieved a very high technical standard.”
The joint rib milling project provides an example from the long-standing development partnership with the CAM provider. The cooling ribs from gearboxes have very deep cavities that entail major risk and are extremely time consuming in programming and machining.
“We opted for OPEN MIND back in 2002 because hyperMILL® best supports our standardisation approach.“
Jörg Wenserski, Head of Engineering at the Machine Centre at the Volkswagen plant in Braunschweig
Rib milling without risk
To this end, the rib milling knowledge management employee group developed a test part that featured all of the known degrees of difficulty, such as nesting, deep cavities, rib intersections, radial ribs and interference contours.
Based on this specification, OPEN MIND subsequently developed a rib milling cycle that introduces a lot of innovations to the machining sequence, such as: an integrated roughing/finishing function, integrated pocket machining of wide ribs, automatic collision detection of the tool holder taking conical milling tools into account and integrated bottom machining. Many of those involved see the fact that the infeed parameters always come directly from the tool database, even in the case of automatically separated areas, as a particular highlight.
In the case of components with a very high degree of ribbing, the new approach made it possible to significantly reduce processing times at the machine. The new rib milling cycle cut pure programming time in half. “In addition to the planned reductions in programming and machining times, we were also able to achieve greater process reliability and considerably reduce tool wear,” says Wolfgang Sofftner, contact partner for 3D machining in component tool engineering.
Customer Story
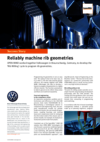
Volkswagen AG | Component Tool Engineering
Braunschweig, Germany