CAM Solution for Wire EDM
The best-in-class OPTICAM wire-cutting module fully integrated in hyperMILL®
OPTICAM can create efficient and flexible NC programs for wire EDM processes regardless of whether it involves simple 2-axis movements or complex 4-axis movements. OPEN MIND now offers the proven OPTICAM wire-cutting module within its hyperMILL® (formerly hyperCAD®-S) CAD software.
Wire EDM works according to the principle of spark erosion and is also referred to as spark erosion or wire cutting. Electro-thermal separation processes are available as an alternative to cutting processes when a low mechanical strain is required to manufacture highly complex geometries. High-precision CNC machines move the tool wire (cathode) with extreme positional accuracy and cut a programmed contour in the workpiece (anode) using spark erosion.
The proven solution for wire EDM
OPTICAM CAM software is used to operate wire electrical discharge machines efficiently and safely. OPTICAM has extensive functions and uses the technology databases from all major manufacturers and up-to-date postprocessors to solve any problem that may be encountered in wire EDM area.
OPEN MIND now provides the fully integrated OPTICAM wire EDM solution in hyperMILL®. As a modern ‘CAD for CAM’ environment, the hyperMILL® CAD system speeds up programming work. It is possible to create milling, mill/turning and wire EDM programs on a single model. All the user needs to do is switch between the OPTICAM wire-cutting module and hyperMILL® CAM software.
The OPTICAM solution meets all user requirements with regard to integration, reliability and user friendliness. This integration makes it a certified product for hyperMILL®
Benefits
- Simple and fast programming of wire electrical discharge machines
- Integrated in a powerful CAD system that allows 3D data to be easily prepared
- Extensive strategies for wire electrical discharge machines with two to four axes
- User-defined strategies can be saved as templates
- Automatic feature generation
- Use of feature information
Brochure
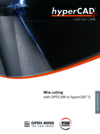
Wire cutting
CAD Integration: OPTICAM in hyperCAD®-S
Features of wire EDM
Feature recognition
Features are automatically linked to the NC program: During component analysis, wire geometries are reliably recognized as features. Faces or edges can also be chosen manually for the wire EDM. Specific areas can be chosen for the creation of user-defined features. The optimal machining strategy is identified for each feature and immediately defined using extensive technology databases.
- Automatic feature generation
- Use of feature information
- Undercut control
- Maximum conicity control
Simulation
The toolpaths can be reliably checked in a 3D simulation. Collision-checked machine and removal simulation makes it possible to closely monitor the workspace and provides a high degree of safety. The path off-setting, clamps and machine heads are all displayed. The cutting time can be quickly and easily calculated for each wire EDM operation. This ensures that machining times can be planned perfectly.
Technology databases
The OPTICAM module is continuously adapted to work in synergy with the latest functions of wire electrical discharge machines. Thanks to its extensive range of functions, the module is the market leader in the field of wire cutting and is recommended by many renowned machine manufacturers. The technology databases are always up to date as they come directly from the machine tool manufacturer.
Postprocessors
The postprocessors are constantly being upgraded by the OPTICAM manufacturer, Camtek. Camtek is always in close cooperation with the machine manufacturers and this ensures that the postprocessors are always up-to-date and reliable.
Optimal strategies
The right strategies for every feature: The optimal machining strategies are identified and immediately defined using extensive technology databases based on their suitability for the machining job. Faces or edges can also be chosen manually for the wire EDM of only specific areas or for the creation of user-defined features. All cuts are shown in the cuts dialog. Toolpaths can be changed afterwards.
Wire EDM strategies:
- Cylindrical machining
- Constant and variable taper – also on cylindrical components
- Ruled face machining with automatic synchronization
- Inclined machining
- Automatic threading and cutting of wires
- Diagonal threading
- Automatic positioning
- Automatic clustering of identical geometries
- Multi-part programming
- Variable reference plane height
Strategies for efficient and reliable wire EDM
- Supervised and unsupervised day and night operation
- Punch strategies
- Reverse cutting
- Automatic cutting-off of slugs
- User-defined strategies can be saved as templates
Pocketing
Collar machining
Ruled face pocketing
Partial pocketing
Allows conventional roughing and pocketing to be combined.
Corner relief
Allows targeted control of the toolpath in sharp interior corners. Five types of corner relief are available without having to spend time changing the model.
Events and segments
Key comments or useful machine instructions can be quickly and easily inserted using event points. Machining operations are divided into individual segments. This way, it is possible to set the number of cuts, offset values, lead on and lead off technologies or partial pocketing separately.
Lead on/lead off
Lead on and lead off technologies can be programmed, including: straight, at an angle, arc-shaped and meander-shaped with the option to overrun the cutting contour.
Start holes and tags
OPTICAM always calculates the optimal start holes and tags, regardless of whether this is fully performed automatically and optimized, pre-defined on the basis of the design or selected manually. Any pre-defined start hole geometries are taken into account. The type, position and number of tags can be defined automatically or manually. Triangular and multiple tags can also be created with multiple start holes.