CAM Software for Production Machining
Highly flexible CAM solutions to efficiently mill different components
Production Machining is a key machining style that is applied to extremely wide range of products. This means CAM solutions have to be highly flexible to efficiently mill different components.
Production machining covers mass-produced components, part family applications and other subcomponents used in complex mechanical assemblies. These components may be machined from solid stock, or machining may be used to finish castings and near-net forgings. Companies operating in this demanding sector face a variety of challenges. These include the need to achieve high standards in terms of component and machining quality as well as constantly reduce programming, setup, and processing times. For companies to remain competitive, they need to be able to efficiently produce high-quality components.

Industry Challenges
-
Shorten setup times
Multiple operations can be simplified using 5‑axis and mill turning technologies
-
Reduce programming times
Thanks to automation made possible by feature and macro technology with holes and pockets
-
Cut machining times
Using innovative HSC and HPC strategies for roughing and finishing
-
Increase process reliability
Through collision-tested toolpaths and reliable simulation technology
-
Improve quality
Optimal surfaces help minimize subsequent finishing processes
hyperMILL® CAD for CAM (formerly hyperCAD®-S)
CAM users in the field of production machining have to process a wide variety of CAD formats quickly and reliably. hyperMILL® features a comprehensive interface package to help them master this task. The CAD software imports all of the product manufacturing information contained in the data.
The “CAD for CAM” solution offers clear advantages: CAM-oriented geometry changes such as the closing of holes as well as other analysis and repair functions can be carried out quickly and easily with the built-in CAD software in hyperMILL®. Practical filter and selection functions ensure that the NC programmer always has a clear overview even with extremely large components.
Would you like to learn more about our complete CAM solution for Production Machining?
If so, please contact OPEN MIND Technologies USA, Inc.
1492 Highland Avenue, Unit 3, Needham MA 02492
CAM Strategies for Industry-specific Components
3D strategies
Indexial Multi-Axis Machining
hyperMILL® MAXX Machining
Mill turning
Probing
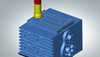
High-feed cutting/high-speed cutting
hyperMILL® offers a large number of functions for HSC and HFC machining. Machining times can be slashed thanks to the use of high feed rate cutters in combination with the ‘adaptive pocket’ function, whereby circular or rectangular pocket geometries are automatically adapted in the area to be machined. In the process, the linear machine movements achieve much higher feed rates.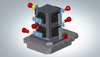
5‑axis multi-axis indexing
All 2.5D machining strategies can also be applied for multi-axis indexing with a fixed tool angle. During this process, the machining orientation is defined using the frame. Simple frame definition and management assist the user in programming machining operations with tilted fourth and fifth axes. With transformations in the NC programs, users can easily and conveniently create programs for multiple components clamped within a single plane or in a tombstone fixture, for instance. All traverse movements are checked for collisions and path-optimized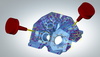
Drilling
hyperMILL® offers a number of strategies for machining a wide variety of hole types. The ‘5‑axis drilling’ function allows drilling jobs with different tool angles to be programmed in a single operation. Tool positions are automatically calculated and the lead-in points to the holes are connected to each other along the optimized path.Mill turning
hyperMILL® MILL-TURN Machining offers a comprehensive strategic package for mill/turn machining for the majority of rotationally symmetrical machine parts and components. All common turning operations as well as special strategies such as 3‑axis simultaneous turning can thereby be freely combined with the milling strategies in a single operating environment.
Increased productivity thanks to hyperMILL®
hyperMILL® makes it possible to quickly create NC programs for use in machining a wide variety of workpieces efficiently and precisely. The hyperMILL® MAXX Machining performance package allows you to save considerable time when roughing and finishing large and small production machining components. For instance, the amount of time required for finishing using a conical barrel cutter can be slashed by up to 90 percent.
In addition to this, multi-axis or complete machining using 5‑axis strategies significantly reduces setup times on the machine.
hyperMILL® MILL-TURN Machining offers a variety of mill/turn strategies for rotationally symmetrical workpieces that deliver maximum precision in a single setup.
Videos: CAM software for Production Machining
hyperMILL® MILL-TURN Machining: Workshop Demo Part
This demo part was made at a hyperMILL® MILL-TURN Machining workshop on a GROB G350T. The combination of milling and turning strategies offers many advantages like increased productivity and flexibility.
Automation made possible by feature and macro technology
The feature and macro technology make it possible to slash programming times. Prismatic components with a large number of holes and pockets can thus be programmed automatically in record time. All fits, threaded holes, and countersinks are detected and taken into account. Stored programming macros can then match proven process workflows to the current geometry.
Advantages at a Glance
-
CAD for CAM
Built-in CAD software (formerly hyperCAD®-S) for optimal component analysis and processing
-
Integrated solution for all machining operations
Milling, drilling, and turning all with a single user interface
-
Optimized roughing and finishing strategies
For efficient, tool- and machine-friendly machining, even when handling materials that are difficult to machine
-
High process reliability
Thanks to perfect milling paths as well as reliable simulation and collision avoidance
-
Easy to program
Intuitive and supported by automated functions
-
High degree of automation
From feature and macro technology through to fully automated programming