CAM Software for Motorsport
Winning teams design and manufacture premium, optimized components to meet a wide array of challenges.
Speed and reliability matter on the racetrack – and for machine tools, too. Manufacturers interested in producing high-end components should choose a high-end CAM system.
Whether they’re riding in racecars or in motorcycles, winning teams design and manufacture premium, optimized components to meet a wide array of challenges. On the racetrack, vehicles battle to outpace one another by hundredths of a second – there’s virtually no room for error. Similarly, component manufacturing calls for achieving the greatest dimensional accuracy, the highest surface qualities, and contour accuracy for free-form surfaces, without making any compromises.
Motorsport involve a particular challenge: Changes to vehicles must be quickly and flexibly implemented so that the teams riding them can start off the next race with better systems on board.

Industry Challenges
-
Extremely high levels of surface quality
Grooves and ridges are taboo; this industry requires milling surfaces that are as smooth as possible to serve as the ideal starting point for subsequent polishing and grinding
-
Large material removal rates
Large amount of material must be removed from the stock of thousand individual parts
-
Dimensional accuracy
Uphold the most stringent tolerances
-
Contour accuracy
Absolutely precise milling of free-form surfaces is required for optimal aerodynamics and to reduce the weight of premium, optimized components
-
Hard-to-machine material
Covers everything across the board – from composites to titanium and Inconel
Videos: CAM software for Motorsport
5-axis Machining: Formula 1 Front Wing
Manufactured by OSG - programmed with CAM software hyperMILL®.
High-end milling
Racing-related applications typically involve challenging geometries for which a great deal of material needs to be machined. hyperMILL® offers sophisticated high-speed cutting (HSC) and high-performance cutting (HPC) strategies that guarantee optimal roughing and finishing processes, even for material that is difficult to machine. This in turn ensures tool- and machine-friendly machining with high material removal rates. The unique 5‑axis HPC strategies from OPEN MIND make it possible for even the deepest cavities to be roughed as quickly as possible and without collisions using short clamped tools. The high-performance finishing module of hyperMILL® MAXX Machining achieves time savings of up to 90 percent, thanks to the use of barrel cutters. It also delivers perfect surfaces.
Would you like to learn more about our complete CAM solution for Motorsport?
If so, please contact OPEN MIND Technologies USA, Inc.
1492 Highland Avenue, Unit 3, Needham MA 02492
CAM Strategies for Industry-specific Components
High-Feed Cutting
Rest Machining
hyperMILL® MAXX Machining
Special Applications
Adaptive pocket/High-Feed Cutting (HFC)
hyperMILL® offers a large number of functions for HSC and HFC machining. Using a freely definable tool geometry makes it possible, for example, to precisely map high-feed cutters, which are then taken fully into account during collision checks and rest material computation. Machining times can be reduced in connection with the ‘adaptive pocket’ function, whereby circular or rectangular pocket geometries are automatically adapted in the area to be machined.
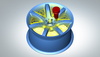
HPC roughing
Trochoidal toolpaths enable efficient roughing of pockets and open areas with large material removal rates. The particularly high axial infeeds and low lateral infeeds ensure tool-friendly roughing with a peeling cut.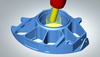
5‑axis helical drilling
Using this strategy, the material is milled from a circular pocket based on helical tilt milling in a 5‑axis simultaneous movement, which is particularly efficient and tool-friendly, even when handling difficult-to-machine materials.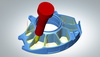
Finishing with Barrel Cutters
This method allows users to achieve time savings of up to 90 percent during tangent plane machining. The use of conical barrel cutters allows for larger line increments while delivering a better surface quality at the same time, compared to conventional finishing methods.Tube package
The ideal solution for intake and exhaust tubes for engines as well as pipe inlets and outlets for pumps and compressors: 5‑axis tube machining makes it possible to machine strongly undercut geometries on the basis of the simplest guide curves. The proven collision check and avoidance system ensures safe 5‑axis milling operations.
Automation using feature and macro technology
Feature and macro technology plays an important role in CAM automation that makes daily work easier for all programmers. hyperMILL® recognizes features such as holes, threads and fittings automatically. These features can be used manually or automatically for NC programming. Macros that can be used to save entire machining sequences enormously reduce the amount of programming required. Programmers’ manufacturing knowledge is stored in the macro database and can be retrieved by all employees at any time. Users can quickly respond to geometry changes using this database. Thanks to standardization and automation, programmers also avoid possible application errors.
Maximum process reliability is a key to success
As it is for delivery times, so it is for racetracks: Speed is decisive in motorsport. Efficient manufacturing with absolute process reliability is necessary in order to uphold tight delivery deadlines and deliver just in time.
When toolpaths are calculated with the hyperMILL® CAM software, the collision check is already incorporated, and reliable simulation technologies make it possible to master the machining of complex 5‑axis integral components at any time.
Advantages at a Glance
-
Innovative roughing and finishing strategies
Particularly efficient as well as tool- and machine-friendly machining, even when handling materials that are difficult to machine
-
Best-in-class 5‑axis strategies
Safe machining of complex components and deep cavities using short, stable tools
-
Complete machining
All machining strategies integrated into a single user interface
-
High degree of automation
From feature and macro technology through to fully automated programming
-
High process reliability
Simulation and collision avoidance for safe processes