Your NC Code Simulation
with All Key CAM Information
hyperMILL® VIRTUAL Machining Center
The hyperMILL® VIRTUAL Machining Center allows you to simulate and analyze the manufacturing process to reduce inefficient operations and costly errors to a minimum.
The hyperMILL® VIRTUAL Machining Center combines the advantages of a CAM data-based simulation with those of an NC code simulation. What you get in the end is an NC code simulation that includes all the process information you need from the hyperMILL® CAM system, such as negative allowances, chamfers, and hole parameters. This information is needed to avoid false collision detection during these machining operations and eliminates the time-consuming task of evaluating the associated collision areas.
Having all of the CAM and machine information is necessary to allow the tool paths to be simulated reliably and completely. A range of different analysis functions lets you accurately assess the subsequent machine run. In this way, the hyperMILL® VIRTUAL Machining Center delivers maximum reliability and significantly increases the efficiency of your machining and set-up processes.
Features
- Based on NC code
- Digital twin of machine
- Visual inspection independent of collision check
- All tool and connecting paths are simulated
- Limit switch check
- Stock removal simulation
- Comprehensive analysis functions
- Machine, holder, tool, model, and blank are checked
- Process information from CAM system
- Networking with the machine
- Optimal component placement
- Clamping test
Process information from the CAM system
Standard simulation systems simulate the machining process using internal tool path data from the CAM system or based on the generated NC code. To reliably and precisely simulate your NC programs, the relevant process information from the CAM system must be evaluated along with the NC code. hyperMILL® is able to do just that. Here’s an example to illustrate this: You program corresponding machining jobs in hyperMILL® and assign negative allowances or machine non-modeled details such as chamfers. Typically, these component violations, which are intentional and by design, are detected as collisions and must be evaluated by you afterwards. But that’s not the case when you’re working with the hyperMILL® VIRTUAL Machining Center. It precisely simulates all machining operations and checks them to ensure maximum reliability.
The following process information is taken into account here:
- Negative allowances
- Trim areas
- Non-modeled details
- Automatic deburring: break chamfers and edges
- Scribing
Simulation with maximum safety
The hyperMILL® VIRTUAL Machining Center offers all the classic options for simulation, embedded in a highly intuitive user interface. The machine simulation is carried out on a digital twin model, taking into account the workpiece, blank, and tool as well as the tool holder, fixtures, and clamps. Axes can be moved manually in the simulation. Axis limitations are indicated and limit switch traversals are detected automatically. Individual machining jobs can be simulated separately or used as a starting point for the simulation.
“The hyperMILL® VIRTUAL Machining Center is key to designing set-up processes in a far more safe and efficient way.”
Dr. Josef Koch
CTO OPEN MIND Technologies AG
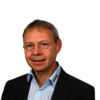
In-depth analysis of the NC program
In addition to efficient simulation, the hyperMILL® VIRTUAL Machining Center provides a wide range of analysis functions that allow you to examine every machining situation in detail. For example, the “Adjust clamping” function makes it possible to check the machining area reliably. It automatically calculates the optimal placement of the component for the available workspace, which can often prevent time-consuming machine adjustments. Various technical charts provide valuable information about the quality of the machine run. All traverse movements of the different axes, feedrates, and spindle speed are visible to the CNC programmer at all times to avoid errors and inefficient operations. The analysis functions therefore provide even greater reliability and transparency in your machining operations.
Analysis Functions in the hyperMILL® VIRTUAL Machining Center
Workspace monitoring
With the help of a stored machine model, the workspace monitoring checks whether any limit switches are traversed by the 2.5D, 3D, 3+2 or 5‑axis simultaneous machining movements. The movements of both the linear axes (X, Y and Z) and the rotary axes (A, B and C) are checked, as well as the clamps and fixturing systems.
Setting breakpoints
The simulation can be controlled to stop at certain locations in order to reliably check critical points and estimate the subsequent processes more precisely. The breakpoints are created automatically under certain conditions, such as a tool change or a change from rapid traverse to cut movements. Moreover, breakpoints can also be selected manually through an NC block line or picked up from any point on the toolpath.
Adjusting visibility
Safe working space analysis
The unique Best‑Fit function automatically optimizes the machining operation to match the available workspace. Workspace monitoring is able to indicate instances where the limit switches have been traversed but the actual workspace is still sufficient for machining. In this case, the Best-Fit function automatically determines the optimal setup location for the respective workspace. This does away with the need for unnecessary setup changes and resulting downtimes.