CAM Software for the Aerospace Industry
The aerospace sector, one of the most demanding industries.
The hyperMILL® CAM software helps manufacturing companies in the aerospace sector gain a critical edge in the face of tough competition.
Complex workpieces, difficult-to-machine materials, and tight time windows are constant companions in the aerospace sector, one of the most demanding industries when it comes to technology. Perfect NC programming across all machining processes is therefore a key prerequisite for companies if they wish to remain competitive in the complex environment of structural, engine, and non-structural aerospace parts.
Innovative Solutions Designed to Meet Tough Challenges
Be it aluminum structural parts, engine components, or non-structural parts for actuation and flight control systems: The hyperMILL® CAM software can solve the challenges of the aerospace industry with ease. hyperMILL® is a comprehensive solution that features intelligent methods and strategies ideally suited to typical aerospace tasks. OPEN MIND is a true innovator and has developed numerous functions that result in perfect component surfaces while also accelerating programming and machining. Complex workpieces, free-form surfaces, deep cavities, and the like can be reliably programmed in the shortest possible time using the HPC, HSC, and 5‑axis solutions provided in hyperMILL®. Even difficult cast and forged parts made of titanium, Inconel and other super-alloys can be machined efficiently and in a tool-friendly manner based on proven HSC and HPC strategies.

Industry Challenges
-
Decreasing setup times
Complete and multi-axis machining using mill-turn and 5‑axis technologies
-
Reduced programming times
Automated NC programming for pockets and holes thanks to feature and macro technology
-
Reduced machining times of material-intense machining jobs
Innovative HSC and HPC strategies for faster roughing and finishing
-
Improved process reliability and safety
Collision-tested toolpaths and state-of-the-art simulation technology
-
Better quality
Blending cycles minimize additional finishing processes
-
Demanding materials
Milling that goes easy on tools and machines thanks to HSC and HPC strategies
hyperMILL® MILL-TURN Machining: Aerospace – Engine Case
This video shows the machining of an engine case for the aerospace industry on a Hermle C42 MT U dynamic. It was programmed using hyperMILL® MILL-TURN Machining strategies combined with high-performance strategies from the hyperMILL® MAXX Machining package such as High-Performance Turning and High-Performance Milling.
The Right Strategy for any Application
hyperMILL® offers a comprehensive range of high-performance machining strategies for every application. The name says it all: The hyperMILL® MAXX Machining performance package offers the perfect strategies for high-performance roughing, finishing, and drilling. For example, exceptionally high metal removal rates can be achieved when roughing thin-walled structural parts. hyperMILL® provides specially developed applications for the efficient manufacture of special aerospace components such as impellers, blisks, and turbine blades.
Complete Machining Is the Baseline
5‑axis machining centers and hybrid machines are the accepted standard for manufacturing companies in the aerospace industry. In addition to other components, a powerful and versatile CAM solution is required to fully exploit the potential of these machines. hyperMILL® combines powerful milling and turning strategies in a single user interface to ensure efficient programming and machining. Required setups are reduced to a minimum, setup times are shortened, and at the same time accuracy is increased.
Fast, Reliable, and Automated Programming
OPEN MIND’s feature and macro technology lays the foundation for automated NC programming. Feature technology can automatically recognize standard geometries such as bores, grooves, and pockets together with all their machining properties. The information obtained is then reused for manual or automated programming by means of stored machining sequences – so-called machining macros. Feature and macro technology not only significantly reduces programming times; this type of standardization also helps to avoid operating errors. If required, programming projects can be executed in a fully automated manner.
Would you like to learn more about our complete CAM solution for the Aerospace Industry?
If so, please contact OPEN MIND Technologies USA, Inc.
1492 Highland Avenue, Unit 3, Needham MA 02492
CAM Strategies for Industry-specific Components
hyperMILL® MAXX Machining
High-Feed-Cutting
Special Applications
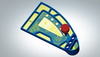
HPC roughing
High-performance roughing with trochoidal toolpaths enables very high material removal rates. This is highly useful, for example, for roughing structural parts as quickly as possible.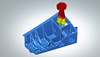
5-axis helical drilling
Using this strategy, the material is milled from a circular pocket based on helical tilt milling in a 5-axis simultaneous movement, which is particularly efficient and tool friendly, even when handling high-strength materials.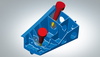
5-axis tangent plane machining
This method allows users to achieve time savings of up to 90 percent during tangent plane machining. The use of conical barrel cutters allows for larger line increments while delivering a better surface quality at the same time, compared to conventional finishing methods.High Speed Cutting (HSC) / High Feed Cutting (HFC)
hyperMILL® offers a large number of functions for HSC and HFC machining. Using a freely definable tool geometry makes it possible, for example, to precisely map high feed cutters, which are then taken fully into account during collision checks and rest material computation. Machining times can be reduced in connection with the ‘adaptive pocket’ function, whereby circular or rectangular pocket geometries are automatically adapted in the area to be machined.
Reliable Simulations Ensure Error-free Processing
‘Safety first’ is of particular importance when producing for the aerospace industry. The hyperMILL® CAM software comes with a powerful NC simulation to ensure that everything will run safely on the machine tool. Collisions are detected in advance and avoided. The advantages are obvious: improved process reliability and fast set-up processes.
The NC code-based simulation of hyperMILL® VIRTUAL Machining allows for the virtual mapping of real machining situations, including the programmable logic controller (PLC) and the machine environment. The simulation already captures and shows users the exact machine movements that will be later performed on the machine tool. The user interface is based on the familiar machine control and is thus very easy to operate. The solution also supports quick familiarization with the simulation. Based on the NC code, hyperMILL® VIRTUAL Machining offers numerous options not only for simulations, but also for analyzing and optimizing the machining processes. CAM software that is tightly integrated with the machine tools is an important prerequisite for realizing Industry 4.0-grade production.
Seamless hyperMILL® PLM Integrations
For aerospace companies that want to combine all product and process data (including NC manufacturing data) into a central PLM environment, hyperMILL® offers corresponding interfaces to leading PLM systems such as Teamcenter, Windchill, or SAP PLM. The CAM system thus enables the networking of the relevant manufacturing disciplines as well as the integration of all CAD, CAM, and NC processes.
OPEN MIND – A Long-standing CAM Partner of the Aviation Industry
In numerous successful projects, OPEN MIND has proven its extensive know-how and shown how components in the aerospace industry can be programmed and processed efficiently. hyperMILL® has also established itself as a CAM system that stands for programming the most complex parts with unprecedented ease, such as impellers and blisks, turbine blades made of high-strength nickel-based alloys, engine housings, and structural parts.
More Videos: CAM software for Aerospace
5-axis Machining: Turbine Blade on GROB
This video shows a machining example of a turbine blade on a GROB G550 machine programmed with the CAM software hyperMILL®.
For more information: turbine blade package
Free OPEN MIND Webinars!
Advantage through knowledge – benefit from our webinar recording and increase your productivity!
Interested in our White Paper for the Aerospace Industry?
PDF: CAM software for Aerospace | 2 MB
Aerospace Solutions
Innovative Solutions Designed to Meet Tough Challenges
Advantages at a Glance
-
Optimum roughing and finishing strategies
That are particularly efficient and ensure tool- and machine-friendly machining, even when handling materials that are difficult to machine
-
Comprehensive best-in-class 5‑axis technology
That enables the safe machining of complex components and deep cavities using short, stable tools
-
Tight dimensional tolerances
To achieve top quality thanks to single clamping made possible by 5‑axis and mill-turning technology
-
Complete machining
All machining strategies integrated in a single user interface
-
High degree of automation
From feature and macro technology through to fully automated NC programming (API)
-
Convenient user interface
CAM solution operated using a single user interface. Intelligent automated functions facilitate intuitive handling.
-
High process reliability
Simulation and collision avoidance for safe machine-based processes
-
High-end postprocessors
Optimally tailored to the customer’s requirements
-
Complete documentation
Simple and well-structured documentation workflow when programming certifiable processes with hyperMILL®